Inhaltsverzeichnis
Wenn es in einem Lager häufig zu Verzögerungen oder Fehlern kommt, ist das ein Zeichen dafür, dass Prozesse nicht optimal ablaufen. Die Gründe dafür können sehr vielfältig sein: eine ungünstige Lagerstrategie, veraltete Maschinen oder die einfache Tatsache, dass verschiedene logistische Prozesse nicht gut ineinandergreifen. An diesen Punkten setzt die Optimierung des Lagers an. Sie zielt darauf ab, ein Lager als Ganzes so effizient wie möglich zu gestalten. Welche Bereiche Sie dafür unter die Lupe nehmen müssen und welche Faktoren wichtig sind, um ein Lager gut zu planen, lesen Sie in diesem Ratgeber.
Definition: Lagerplanung umfasst die systematische Abstimmung aller im Lager stattfindenden Prozesse mit dem Ziel, eine möglichst effiziente Lagerung und Bewegung von Waren oder Gütern zu erzielen.
Warum es wichtig ist, ein Lager gut zu planen
Durch kluge Umstrukturierungen und die Automatisierung von Lagerabläufen lässt sich die Wirtschaftlichkeit eines Lagers deutlich erhöhen. So können etwa moderne Kommissionierverfahren wie Pick-by-Vision oder Pick-by-Voice dazu beitragen, das Picking möglichst fehlerarm und zeitsparend zu gestalten. Für Ihren Betrieb bedeutet das ganz praktisch: Sowohl das Lager selbst als auch das Budget für die Lagerhaltung werden optimal genutzt, wodurch Sie langfristig Ihre Kapazitäten erhöhen und Kosten sparen können. Denken Sie auch daran, alle Vorkehrungen zum Arbeitsschutz für Ihr Lager zu treffen, um die Sicherheit Ihrer Mitarbeitenden zu gewährleisten.
Eine übergreifende Abstimmung aller Abteilungen ist wichtig für ein effektives Ergebnis. Wenn Sie Strategien beispielsweise nur für die Optimierung des Versands oder der Kommissionierung anwenden, andere Bereiche wie den Wareneingang oder den Warenausgang aber unverändert lassen, kann das gewünschte Ergebnis einen gegenteiligen Effekt haben.
Die Lagerplanung betrifft nicht nur Neubauten wie etwa die Errichtung von Logistik-Hubs. Auch in bestehenden Lagern sollten Ausstattung und Prozesse regelmäßig analysiert werden, um zu sehen, ob sich die Effizienz durch technische Neuerungen oder Veränderungen in den Betriebsabläufen steigern lässt.
Diese Grundsätze sollten Sie bei der Lagerplanung beachten
Folgende Punkte sollten Sie berücksichtigen, um ein möglichst effizientes Lager zu planen:
Flexibilität: Das Lagerdesign sollte sich Veränderungen im Geschäftsbetrieb anpassen können, beispielsweise steigenden Lagervolumina oder neuen Produktlinien.
Sicherheit: Sorgen Sie dafür, dass alle Voraussetzungen gegeben sind, damit gesetzliche Vorschriften zur Sicherheit im Lager eingehalten werden können.
Zugänglichkeit: Alle Artikel sollten leicht erreichbar sein.
Durchflussoptimierung: Minimierung der zurückgelegten Wege und Zeiten für den Warenein- und -ausgang.
Bestandskontrolle: Einfache und genaue Überwachung und Verwaltung von Lagerbeständen.
Skalierbarkeit: Das Design sollte Erweiterungen oder Anpassungen ohne größere Umstrukturierungen ermöglichen.
Nachhaltigkeit: Berücksichtigen Sie Umweltaspekte, z. B. die Energieeffizienz Ihrer Flurförderzeuge und Richtlinien zur gewerblichen Abfallreduktion.
Kostenbewusstsein: Alle Entscheidungen sollten Sie unter Berücksichtigung der langfristigen Betriebskosten und der Investitionsrendite treffen.
Technologieeinsatz: Integrieren Sie nach Möglichkeit moderne Technologien, z. B. automatisierte Systeme oder Lagerverwaltungssoftware (LVS), um Ihre Prozesseffizienz zu steigern.
Lagerplanung: So ist der Ablauf
In der Praxis fließt die Lagerplanung üblicherweise in die gesamte Unternehmungsplanung mit ein. Für ein systematisches Vorgehen schauen Sie sich alle Lagerbereiche an und ermitteln zunächst für jeden einzeln das Optimierungspotenzial. Anschließend konzentrieren Sie sich auf die Intralogistik und koordinieren das Zusammenspiel der verschiedenen Bereiche.
Konkret geht es dabei um vier Faktoren:
- Ziele festlegen
Für die Lagerorganisation legen Sie fest, wie die Logistikprozesse im Lager ablaufen sollen. Dazu gehören die Ein- und Auslagerung von Waren, die Steuerung der Materialflüsse und die Lagerstrategie, nach der die Waren eingelagert werden. Ziel ist es, eine optimale Balance zwischen Ausnutzung der Lagerfläche und kurzen Beförderungswegen zu finden.
- Welche Technik ist die richtige?
Bei der Bestimmung der Lager- und Transporttechnik geht es um die Art der Bedienung und die Ausstattung mit geeigneten Regalsystemen. Beide hängen stark voneinander ab: Während Sie in einem voll automatisierten Lager keinen direkten Zugriff zu den Regalen brauchen, können Sie darauf nicht verzichten, wenn Sie das Lager mit Flurförderzeugen wie Staplern oder Hubwagen bedienen.
- Anforderungen an das Lager
Untersuchen Sie, wie die Lagereinheiten üblicherweise aussehen. Wie groß und schwer sind sie? Handelt es sich um Stück- oder Schüttgut? Benötigen Sie Hilfsmittel wie Paletten, Lagerbühnen oder Lagerbehälter? Daraus lassen sich Platzbedarf und ggf. spezielle Anforderungen an den Lagerplatz ableiten, z. B. Schwerlastregale für schwere Güter, Auffangwannen für die Gefahrgutlagerung oder spezielle Bereiche für die Palettierung.
- Das Lagerlayout
Ganz zum Schluss der Lagerplanung entwerfen Sie das Lagerlayout, indem alle vorherigen Aspekte (Logistik, Technik, Einrichtung und Lagereinheiten) möglichst optimal aufeinander abgestimmt werden.
• Entwerfen Sie zunächst ein Groblayout für die Anordnung der verschiedenen Bereiche.
• Details legen Sie in einem zweiten Schritte fest: Ausrichtung der Regale, Fördertechnik und Bedienwege.
Verschiedene Bereiche im Lager planen
Je größer ein Lager ist, umso komplexer wird auch die Planung, denn es gibt verschiedene Abteilungen und Aufgaben, die Sie optimieren und miteinander in Einklang bringen müssen. Das wird leichter, wenn Sie verwandte Abläufe in Lagerbereichen zusammenfassen. Für eine grobe Einteilung von Lagerzonen können Sie die Bereiche Lagerinfrastruktur, Fördermittel, Materialflüsse definieren.
Üblicherweise ist folgende Unterteilung sinnvoll:
- Warenannahme
- Qualitätskontrolle
- Anpassung von Ladeeinheiten
- Lagerung
- Auftragserfassung
- Warenversand
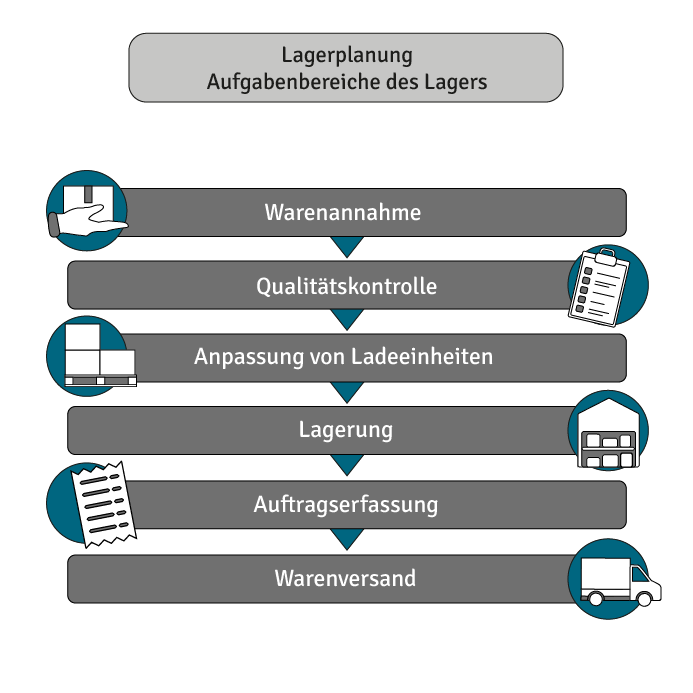
Planung des Annahmebereichs
Die Warenannahme ist die erste Station, die Güter auf dem Weg zur Einlagerung passieren müssen. Der Bereich sollte deshalb möglichst direkt am Lagereingang bzw. an der Entladestation geplant werden. Hier werden die Lieferungen geprüft und mit den Bestellungen abgeglichen. In unmittelbarer Nähe sollte sich auch eine Station zur Qualitätskontrolle befinden, die dann, falls erforderlich, in einen Bereich zur Anpassung der Ladeeinheiten übergeht. Vermeiden Sie in diesem Abschnitt lange Beförderungswege oder greifen Sie auf automatisierte Lösungen zurück. Hierfür bieten sich unter anderem Palettenfördersysteme, Fließbänder oder Rollenbahnen an. So können Sie Zeit, Arbeitskraft und Ausgaben einsparen.
Bei Größe und Ausstattung des Annahmebereichs orientieren Sie sich an den für Ihren Betrieb üblichen Anlieferungsmengen. Falls Menge und Umfang der Lieferungen stark schwanken, ist eine Teilung sinnvoll, sodass ein Bereich der Warenannahme immer in Betrieb ist, während der zweite nur bei größeren oder außerplanmäßigen Liefereingängen betrieben wird. Denken Sie daran, auch für diesen Fall Arbeitsmittel, Werkzeuge und vor allem qualifizierte Mitarbeiter bereitzustellen.
Planung des Lagerbereichs
Wie Sie die eigentlichen Lagerflächen am besten planen, lässt sich kaum allgemein darstellen, denn dies hängt von unterschiedlichen Faktoren ab. Je nachdem, welche Arten von Lagergütern in Ihrem Betrieb anfallen, wie hoch die Umschlagsrate der Waren ist, welche Mengen täglich ein- und ausgehen, sind jeweils andere Lagersysteme geeignet. Zwei grundlegende Aussagen lassen sich allerdings treffen:
- Für Waren, die lange im Lager verbleiben und in geringen Mengen beschafft werden, empfiehlt sich eher die manuelle Kommissionierung in geeigneten Fachbodenregalen und ein Lagerplatz an der Peripherie.
- Waren, die in großen Mengen eingehen und auch kurzfristig wieder abgesetzt werden, sollten leicht zugänglich sein und auf kürzestem Weg zur Versandabteilung transportiert werden. In diesem Fall können automatisierte Kompaktlagersysteme das Maximum an Lagerfläche und Geschwindigkeit bei der Kommissionierung herausholen.
Bei der Entscheidung für ein Lagersystem spielen auch wirtschaftliche Überlegungen eine Rolle. Die Investitionskosten für automatisierte Lösungen sind hoch, können sich aber bei entsprechend höherem Warenumschlag und der langfristigen Einsparung von Kosten für die Lagerhaltung durchaus lohnen.
In der Praxis werden deshalb häufig gemischte Lagerkonzepte umgesetzt. Das bedeutet, dass mehrere Bereiche mit unterschiedlichen Regalarten, Bediensystemen und Fördermitteln ausgestattet werden (manuell, halb automatisiert, voll automatisiert) und die Lagergüter je nach Umschlagsrate in den geeigneten Lagerbereich verteilt werden.
Planung des Versandbereichs
In diesem Bereich des Lagers sollte viel Platz herrschen, denn hier erfolgt sowohl die Zusammenstellung der Warenlieferungen als auch die Verpackung und Klassifizierung der Liefereinheiten.
Im ersten Schritt brauchen Sie eine Station zur Auftragserfassung. Nutzen Sie eine Software für Lagerverwaltung und Logistik, können Sie damit sofort die Verfügbarkeit der Waren prüfen, die Zusammenstellung der Lieferung in Auftrag geben und den Versandtermin bestimmen. Ohne IT-Unterstützung müssen diese Schritte einzeln erfolgen.
Sind die Waren für den Versand bereit, werden Sie manuell oder mit maschineller Unterstützung (z. B. durch Verpackungsroboter, Maschinen für Füllmaterial, etc.) in größere Transporteinheiten zusammengefasst und verpackt. Anschließend erfolgt die Gruppierung nach Kunden, Aufträgen oder Transportrouten in einem gesonderten Bereich des Lagers, der sich wiederum möglichst nah an der Laderampe für die Beladung der Container oder Lkws befinden sollte.
FAQ zum Thema Lagerplanung
Für eine umfassende Optimierung müssen Sie ausnahmslos alle Einrichtungen und Abläufe berücksichtigen, wenn Sie Ihr Lager planen oder modernisieren. Konkret geht es dabei um vier Faktoren:
1. Lagerorganisation: Wie laufen die internen Logistikprozesse im Lager ab?
2. Lager- und Transporttechnik: Welche Lagersysteme und Fördermittel eignen sich am besten für Ihre Waren?
3. Lagereinheiten: Wie sind übliche Lagereinheiten beschaffen (Größe, Gewicht, Form, etc.) und welche Anforderungen entstehen dadurch an den Lagerplatz?
4. Lagerlayout: Wie müssen Arbeitsbereiche und Lagereinrichtung angeordnet werden, damit die Intralogistik optimal funktioniert?
Je größer ein Lager ist, umso komplexer wird auch die Planung, denn es gibt verschiedene Abteilungen und Aufgaben, die Sie optimieren und miteinander in Einklang bringen müssen. Das wird leichter, wenn Sie verwandte Abläufe in Lagerbereichen zusammenfassen. Üblicherweise sind das:
• Warenannahme
• Qualitätskontrolle
• Anpassung von Ladeeinheiten
• Lagerung
• Auftragserfassung
• Warenversand
Falls Sie eine gröbere Einteilung bevorzugen, können Sie die Bereiche Annahme, Lagerung und Versand definieren.
Für eine systematische Lagerplanung schauen Sie sich alle Lagerbereiche an und ermitteln zunächst für jeden einzeln das Optimierungspotenzial. Anschließend konzentrieren Sie sich auf die Intralogistik und koordinieren das Zusammenspiel der verschiedenen Bereiche. Eine umfassende und übergreifende Abstimmung aller Abteilungen ist angebracht.
Bildquellen:
© gettyimages.de – Morsa Images