Inhaltsverzeichnis
Ob Sie ein neues Lager planen oder die Effizienz des bestehenden Lagers ermitteln wollen, in beiden Fällen müssen Sie die aktuelle und die optimale Lagerkapazität für Ihren Betrieb kennen. Sie stellt die Basis für alle folgenden Planungs- und Arbeitsschritte dar. Wie Sie die Lagerkapazität richtig berechnen, welche Faktoren dabei eine Rolle spielen und in welchen Fällen Sie die Arbeit besser einer Software überlassen, erfahren Sie in diesem Ratgeber.
Was ist die Lagerkapazität und wofür ist sie wichtig?
Die Lagerkapazität beschreibt, wie viel Platz in einem Raum für die Lagerung von Gütern zur Verfügung steht. Sie dient als Grundlage, um vorhandene Lagerflächen möglichst optimal auszunutzen oder einen geeigneten Lagerraum für die erforderliche Menge an Rohstoffen und Produktionsgütern eines Unternehmens zu finden. Das macht sie zu einer äußerst wichtigen Größe für eine effiziente Lagerhaltung und damit letztendlich auch für eine wirtschaftliche Betriebsführung.
Wenn Sie die maximale Lagerkapazität berechnen, können Sie den tatsächlichen und den aktuell genutzten Lagerraum gegenüberstellen. Auf diese Weise sehen Sie, ob Sie den vorhandenen Platz optimal ausnutzen oder ob möglicherweise Optimierungspotenzial besteht. Entdecken Sie dadurch größere Differenzen, können Sie mit entsprechenden Maßnahmen zur Lagerplanung
- die Lagerkosten senken
- den Lagerbestand optimieren
- die Lagerkapazität erhöhen
- die Effizienz des Lagers verbessern
Umgekehrt hilft Ihnen eine Berechnung der benötigten Lagerkapazität für Ihre Rohstoffe und Waren dabei, zukünftige Erweiterungen des Lagers oder einen Neubau von vorneherein optimal zu planen.
Berechnung der Lagerkapazität
Die Größe von Gebäuden und Lagerhallen wird häufig in Quadratmeterzahlen angegeben. Diese sind jedoch nicht zur Berechnung der Lagerfläche geeignet, denn mit Regalen, Tribünen und Lagerbehältern nutzen Sie mehrere Ebenen in einem Lagerraum. Um die tatsächliche Größe zu berechnen, müssen Sie deshalb nicht nur die Grundfläche, sondern auch die Höhe berücksichtigen.
Die absolute Lagerkapazität berechnen Sie mit der Formel:
- Lagerkapazität = Lagerfläche x Lagerhöhe
Beispiel: Eine Lagerhalle ist 15 m breit, 60 m lang und 5 m hoch.
Lagerfläche: 15 m x 60 m = 900 m2
Lagerkapazität: 900 m2 x 5 m = 4.500 m3
Allerdings werden im Betriebsalltag nicht alle Flächen in einem Gebäude zur Lagerung genutzt. Oft gibt es Bereiche für die Bearbeitung von Logistikprozessen wie Wareneingang und Warenausgang sowie Büros, Umkleide- und Versorgungsräume. Sie müssen also in einem ersten Schritt zunächst die tatsächliche Lagerfläche berechnen. Dazu dient die Formel:
- Lagerfläche = Gesamtfläche – nicht zur Lagerung genutzte Flächen
Beispiel: Von der oben berechneten Lagerfläche werden folgende Nutzflächen abgezogen:
Arbeitsflächen: 160 m2
Transportwege: 210 m2
Büros: 30 m2
Umkleiden und Sanitäranlagen: 75 m2
Nutzflächen: 160 m2 + 210 m2 + 30 m2 + 75 m2 = 475 m2
Tatsächliche Lagerfläche: 900 m2 – 475 m2 = 425 m2
Mit diesem Ergebnis wird die Lagerkapazität mit der oben genannten Formel neu berechnet:
Lagerkapazität: 425 m2 x 5 m = 2.125 m3
Auf diese Weise erhalten Sie also die tatsächlich zur Verfügung stehende Lagerkapazität und können die passende Lagerausstattung wählen, um den Raum optimal auszunutzen.
An diesem Punkt kommt eine weitere Herausforderung auf Sie zu. Selbst wenn Sie den Raum mit robusten Schwerlastregalen, platzsparenden Lagerbehältern und speziellen Lösungen zur Kleinteileaufbewahrung ausstatten, gibt es in der Höhe freibleibende Flächen, etwa für Lüftungsanlagen oder Elektrik. Dieser ungenutzte Raum wird in der Logistik Leerraum genannt und sollte ebenfalls berechnet und von der Lagerkapazität abgezogen werden, um ein möglichst akkurates Ergebnis zu erhalten.
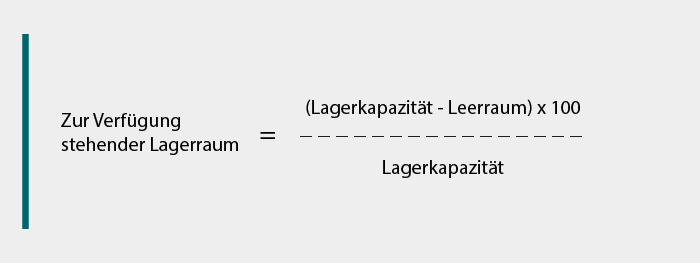
Beispiel: Gehen wir nun davon aus, dass in der Lagerhalle 1,50 m unter dem Dach frei bleiben, muss mit dieser Zahl der Leerraum der tatsächlichen Lagerfläche berechnet werden.
Leerraum: 425 m2 x 1,50 m = 637,50 m3
Diese Zahl wird nun in die Formel für den zur Verfügung stehenden Lagerraum eingesetzt:
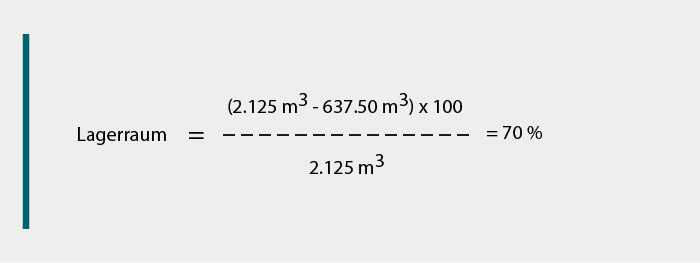
Das Ergebnis ist eine Prozentzahl, die aussagt, wie viel Prozent der Lagerkapazität tatsächlich genutzt wird. Sie sollte möglichst hoch sein und, falls nötig, mit geeigneten Maßnahmen verbessert werden.
Faktoren mit Einfluss auf die Lagerkapazität
An den genannten Nebenrechnungen sehen Sie, dass eine exakte Berechnung der tatsächlichen Lagerkapazität nicht so einfach ist. Die Formel erlaubt streng genommen nur Annäherungswerte. Neben den bereits erwähnten Faktoren wie Art der Regale oder Aufbewahrungsbehälter gibt es weitere Parameter, die Einfluss auf eine effiziente Nutzung von Lagerflächen haben:
- Art der Lagergüter (Flüssigkeiten, Schüttgüter oder Stückgüter) und damit verbundene Platzanforderungen
- Menge und Vielfalt der Lagergüter: Lagern Sie viele verschiedene Einzelgüter (zum Beispiel eine Vielzahl an Rohstoffen zur Versorgung der Produktion) oder große Mengen gleichförmiger, versandfertiger Güter?
- Sicherheitsvorschriften, etwa bei der Lagerung von Lebensmitteln, Gefahrgut oder Gefahrstoffen
- Einsatz von Paletten: Einschränkungen an Traglast und Beladung können Leerräume in einzelnen Regalfächern verursachen
- zusätzliche Lagercontainer auf dem Betriebsgelände
- Lageraufbau: kompaktes, voll automatisiertes Zentrallager oder einzeln zu bestückendes Palettenlager
- Organisation der Lagerlogistik (Transportwege und -methoden, Lagerstrategie, etc.)
Die gewählte Lagerstrategie bestimmt die Lagerplätze der einzelnen Güter. Unter bestimmten Umständen wirkt sie sich auf die Auslastung des Lagers und damit auch auf die tatsächlich zur Verfügung stehende Kapazität aus. Beispielsweise hat bei der First-in-First-out-Methode (FiFo) in einem Transitlager der Zeitpunkt des Wareneingangs eine größere Bedeutung als der Platzbedarf im Lager. Das kann dazu führen, dass einige Lagerflächen ungenutzt bleiben oder nicht vollständig ausgenutzt werden, während andere vollkommen ausgelastet sind. Aus diesem Grund ist es so wichtig, die für den Betrieb wirtschaftlich effektivste Strategie herauszufinden.
Lagerkapazität berechnen mit Formel oder Software?
Wenn Sie die Berechnung der Lagerfläche und -kapazität mit Papier und Stift erledigen wollen, ist es schwierig und aufwendig, den Einfluss der oben genannten Faktoren in konkrete Zahlen zu übersetzen. Für kleinere Betriebe mit einem übersichtlichen Lagerraum und wenigen Lagergütern ist es durchaus machbar. Sobald Lagergröße und die Produktvielfalt zunehmen, leistet eine Lagerverwaltungssoftware (LVS) unschätzbare Dienste. Sie kann alle benötigten Werte unter Berücksichtigung des aktuellen und vergangenen Lagerbestands berechnen. So haben Sie in wenigen Sekunden alle relevanten Größen parat, um die für Ihren Betrieb benötigte Lagerfläche zu berechnen.
Ein weiterer Vorteil der Software ist, dass sie auch andere wichtige Lagerkennzahlen schnell und unkompliziert zur Verfügung stellt. Dazu gehören:
- Lagerbestand (Mindest- und Meldebestand)
- Lagerumschlagzahlen
- Lagerdauer
- Kapitalbindung
- Lagerkosten
- Produktivität
- Wareneinsatz
Ein umfassendes Lagerverwaltungssystem liefert Ihnen nach einer gezielten Abfrage sowohl Einzel- als auch Durchschnittswerte, kann Entwicklungskurven abbilden und auf der Basis vergangener Werte sogar Prognosen geben. Damit können Sie weit mehr als nur die tatsächliche und benötigte Lagerkapazität berechnen. Sie haben jederzeit im Blick, ob Ihr Lager effizient arbeitet, und können bei Problemen zeitnah Maßnahmen zur Optimierung einleiten, indem Sie Ihr Lager neu organisieren, Lagerflächen erweitern oder die Arbeitsabläufe optimieren.
FAQ zur Berechnung der Lagerkapazität
Die Lagerkapazität gibt an, wie viel Platz in einem Raum zur Lagerung genutzt werden kann bzw. für die Lagerung einer bestimmten Anzahl von Gütern nötig ist. Sie ist eine wichtige Größe, um
· die benötigte Lagerfläche zu berechnen
· die Auslastung eines Lagers zu bestimmen
· den vorhandenen Lagerraum optimal auszunutzen
Die Grundfläche eines Lagers zu bestimmen ist einfach, bei der Lagerkapazität wird es schwieriger, weil sie neben der Raumhöhe von weiteren Faktoren bestimmt wird, etwa:
· Lagergut (Art, Menge, Vielfalt)
· Lagerbehälter und Paletten (Art, Traglast, Ausnutzung)
· Lagereinrichtung
· Lageraufbau und Transportwege
· Lagerstrategie
· Sicherheitsvorschriften
Diese Faktoren haben im Betriebsalltag Einfluss darauf, wie gut sich der vorhandene Lagerraum ausnutzen und optimieren lässt.
Die eigentliche Berechnung der Lagerkapazität ist recht einfach. Sie ergibt sich aus der Formel:
Lagerkapazität = Lagerfläche x Lagerhöhe
Schwierig wird es dadurch, dass Sie alle Flächen, die nicht zur Lagerung genutzt werden können, abziehen müssen. Dazu gehören unter anderem Arbeitsbereiche, Umkleiden, Toiletten, Büros, etc.
Lagerfläche = Gesamtfläche – nicht zur Lagerung genutzte Flächen
Gleiches gilt auch für die Höhe. Hier wird der Platz, den Lüftung und Klimaanlage oder Beleuchtung einnehmen, als Leerraum abgezogen. Erst dann lässt sich die Lagerkapazität möglichst exakt berechnen.
Bildquellen:
Jungheinrich AG