Inhaltsverzeichnis
Kommissionierung ist eine der zentralen Aufgaben im Lager. Der Prozess umfasst sämtliche Arbeitsschritte, die für die Zusammenstellung von Artikeln und Rohstoffen nach einer Bestellung nötig sind. Die hierbei angewandten Methoden beeinflussen zahlreiche Faktoren, beispielsweise den Aufbau des Lagers, die Zuteilung von Lagerplätzen, die Organisation der Intralogistik oder die Wahl geeigneter Fördertechnik.
Im Ratgeber erhalten Sie einen Überblick über diese Zusammenhänge und die wichtigsten Informationen zur Kommissionierung: Welche Arten es gibt, zu welchen Betriebsformen sie passen und wie sie in der Praxis umgesetzt werden können.
Was ist Kommissionierung? Aufgaben und Definition
In der Logistik ist die Kommissionierung laut Definition ein Vorgang, bei dem einzelne Güter oder Artikel aus dem Gesamtsortiment eines Unternehmens zu einer Warensendung zusammengestellt werden. Sie ist ein wichtiger Bestandteil der Auftragsabwicklung und erfolgt auf der Grundlage von Bestellungen, die entweder direkt von der Kundschaft oder intern von einer anderen Abteilung des Unternehmens (z. B. aus der Produktion) stammen. Mitarbeitende, die diese Aufträge im Lager bearbeiten, werden als Kommissionierende oder auch Pickerinnen und Picker bezeichnet.
Gemeinsam mit Wareneingang, Lagerung, internem Gütertransport, Umschlag und Warenausgang ist die Kommissionierung ein Teilbereich der Intralogistik. Sie umfasst wiederum verschiedene Prozesse, darunter
- die Lokalisierung der bestellten Artikel in verschiedenen Lagerzonen
- die Wahl geeigneter Fördermittel, Transportwege, Behälter, etc.
- die Entnahme der Ware aus dem Lagerregal
- die Zusammenstellung der Warensendung
- den Transport vom Lagerplatz zum Verpackungs- und Versandbereich
Je nachdem, wie komplex die Bestellungsabwicklung in einem Betrieb ist, kann die Kommissionierung unterschiedlich gestaltet werden. Ein entscheidendes Kriterium für den Ablauf ist, ob ein Betrieb größtenteils regelmäßige, planbare Aufträge erfüllt oder eher kurzfristige, individuelle Einzelbestellungen bearbeitet. Auch andere Parameter wie Warenvielfalt, Größe des Lagers, Umfang der Sendungen sowie Art und Größe der Versandgüter spielen eine Rolle. Für jedes Szenario gibt es geeignete Systeme und eine optimale Methode, um die Kommissionierung möglichst effizient zu organisieren.
An den Kommissionierzeiten lässt sich ablesen, wie schnell Aufträge im Lager bearbeitet werden. Daher besteht hier ein großes Optimierungspotenzial, wenn Sie Ihre Lagerprozesse effizienter gestalten möchten.
Kommissionierungsmethoden zur effizienten Bearbeitung von Aufträgen
Um die optimale Methode zur Kommissionierung zu finden, sind die eingehenden Bestellungen essenziell. Aus den Bestellmengen, der Anzahl der verschiedenen Posten und eventuellen Wiederholungen der Bestellung können Sie ableiten, welche Kommissionierungsmethode sich für die reibungslose Abwicklung am besten eignet. Sie haben die Wahl zwischen ein- oder zweistufigen Verfahren, die Sie bereits bei der Lagerplanung berücksichtigen können.
1. Die einstufige Kommissionierung
Die einstufige Kommissionierung erfolgt für jeden Auftrag einzeln. Das heißt, es werden alle Einzelposten einer Bestellung aus dem Lager entnommen und zur Verpackung weitergegeben, bevor der nächste Auftrag an der Reihe ist. Dieses Verfahren ist in erster Linie auftragsorientiert, kann aber in der Praxis auf zwei verschiedene Arten umgesetzt werden.
- Auftragsorientierte, serielle Kommissionierung:
Alle bestellten Artikel werden einzeln und der Reihe nach vom entsprechenden Lagerplatz geholt. Je nach Größe des Lagers ist dafür eine Person zuständig, die das ganze Lager durchläuft. Alternativ kann der Auftrag von einer Lagerzone zur nächsten weitergegeben werden. Diese Methode kommt häufig vor, ist jedoch nur in kleineren Betrieben mit überschaubaren Lagerräumen sinnvoll.
Denn je größer Aufträge und Lager sind, umso mehr überwiegen die Nachteile: Während die erste Variante mit langen Wegen und Kommissionierzeiten verbunden ist, kann es bei der zweiten zu langen Wartezeiten und Fehlern bei der Übergabe kommen.
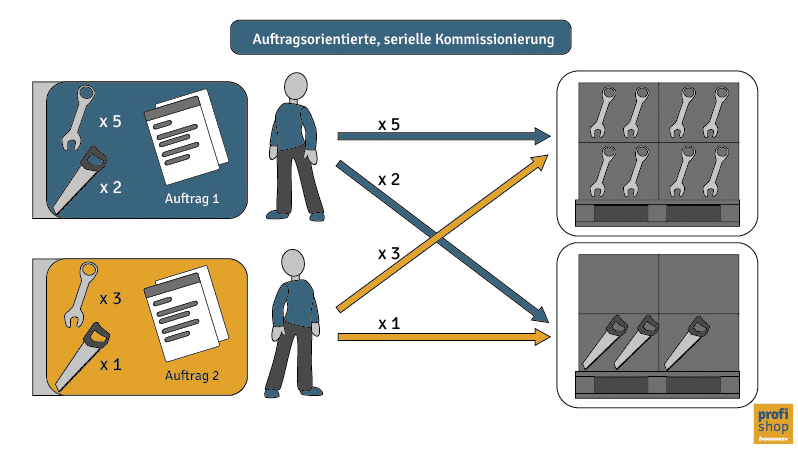
- Auftragsorientierte, parallele Kommissionierung:
Hier arbeitet die Belegschaft in mehreren Lagerzonen gleichzeitig an der Abwicklung eines Auftrags. Die Zusammenstellung der Sendung erfolgt an einer Sammelstelle, hier treffen alle Einzelposten der Bestellung ein. Mit dieser Methode verkürzen sich die Kommissionierzeiten. Sie hat jedoch den Nachteil, dass ein zusätzlicher Arbeitsbereich für die Zusammenführung der Waren erforderlich ist. Auch ist die Koordination im Vorfeld aufwendig, um den Auftrag aufzuteilen und unnötige Wartezeiten und Leerläufe in den einzelnen Lagerzonen zu vermeiden.
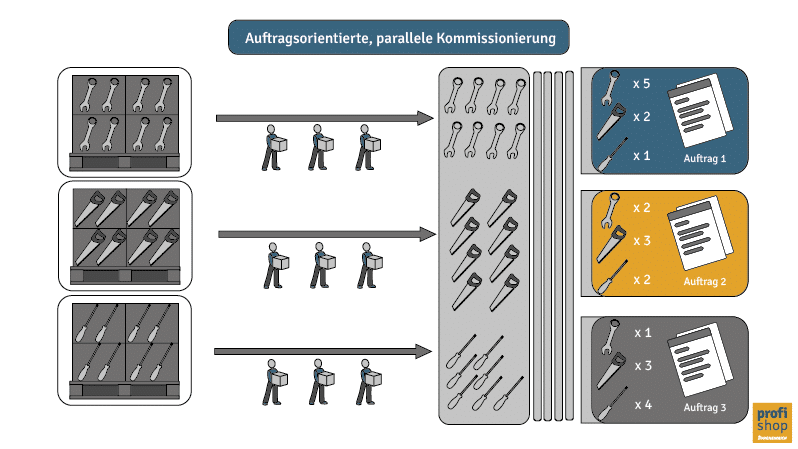
2. Die zweistufige Kommissionierung
Gehen mehrere Bestellungen für die gleichen Produkte ein, ist die zweistufige Kommissionierung die bessere Wahl. Bei diesem Verfahren werden mehrere Aufträge gleichzeitig bearbeitet. Die zu versendende Gesamtmenge der Produkte wird aus dem Lager entnommen und erst in einem zweiten Schritt auf die einzelnen Lieferungen aufgeteilt.
Dieses Verfahren nennt sich auch serienorientierte, parallele Kommissionierung oder Multi-Order Picking. Es bewirkt, dass sich die für die Kommissionierung benötigten Wegstrecken und Wegzeiten deutlich verringern, weil die jeweiligen Lagerplätze und -zonen seltener angesteuert werden müssen. Das heißt jedoch nicht, dass ein Auftrag tatsächlich schneller erledigt wird, da erst mehrere Aufträge zusammenkommen müssen. Die Methode lohnt sich somit erst ab einem größeren Auftragsvolumen.
Ein Nachteil für kleinere Betriebe ist der hohe Organisationsaufwand. Die Aufträge müssen zunächst nach bestellten Waren zusammengefasst, gleichzeitig an die betroffenen Lagerzonen weitergeleitet und anschließend wieder in einzelne Lieferungen aufgeteilt werden. Große Versandunternehmen profitieren hingegen von der Methode, denn sie ist sehr gut in einem automatisierten Lager umsetzbar, in dem eine leistungsfähige Verwaltungssoftware das Management von Bestellungen und Versand übernehmen kann.
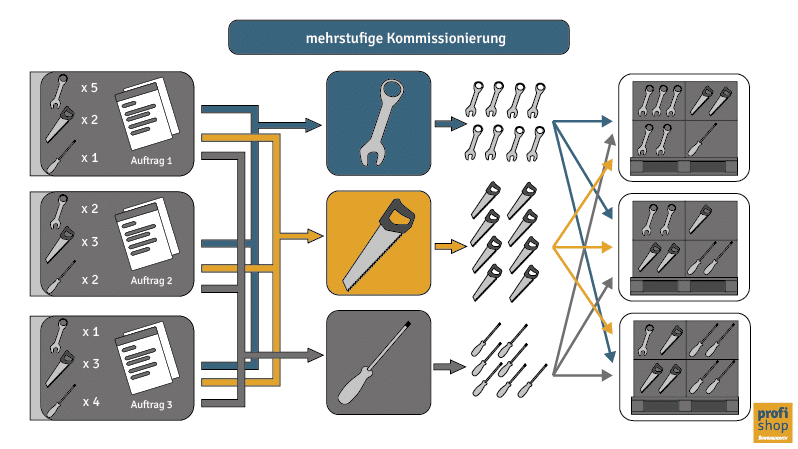
Kommissionierungssysteme: Wie kommen Mensch und Ware zusammen?
Eine grundsätzliche Entscheidung im Rahmen der Lagerplanung ist, wie Sie die Waren kommissionieren wollen. Stellen Sie Warensendungen manuell zusammen oder setzen Sie auf die automatische Kommissionierung?
Die Antwort auf diese Frage hat Einfluss auf Einrichtung und Ausstattung des Lagers, aber auch auf die Wahl einer geeigneten Lagerstrategie, denn sie entscheidet, wie das Personal an die zum Versand vorgesehenen Güter kommt. Dafür gibt es zwei Möglichkeiten:
- Die Mann-zur-Ware-Kommissionierung steht für die manuelle Kommissionierung. Die zuständige Lagerfachkraft bewegt sich zum Lagerplatz der Ware und entnimmt die bestellte Menge. Das erfolgt entweder ganz ohne Hilfsmittel, meistens aber mithilfe manuell betriebener Flurförderzeuge.
- Bei der Ware- zum-Mann-Kommissionierung erfolgt eine Zusammenstellung der einzelnen Güter durch halb- oder vollautomatische Kommissionierung. Die gewünschten Waren werden direkt zu einem festgelegten Kommissionierungsplatz gebracht. Je nach Grad der Automatisierung des Lagers erfolgt die Bedienung durch Menschen oder durch softwaregesteuerte Regalbediengeräte oder Kommissionierroboter.
Die erste Variante erlaubt ein großes Maß an Individualisierung und ist deshalb vor allem für Betriebe mit einem hohen Anteil an Einzelbestellungen geeignet. Leistungsfähige Hubwagen, Hochhubwagen und Gabelstapler befördern auch größere Warenmengen und können gleichzeitig flexibel und bedarfsorientiert eingesetzt werden.
Automatisierte Lösungen eignen sich hingegen optimal für die zeit- und ressourcensparende Abwicklung planbarer Großaufträge mit relativ kleinartigen Waren, etwa im Hochregallager oder im Schmalganglager. Ein Regalsystem aus hochbelastbaren Schwerlastregalen nutzt die Lagerfläche optimal aus und kann mit der passenden Fördertechnik vollkommen automatisch bewirtschaftet werden.
Welche Kommissioniermethoden gibt es?
Kommt in Ihrem Lager die manuelle Kommissionierung zum Einsatz, müssen Sie sich für ein Verfahren zur Anzeige und Dokumentation der Warenentnahme entscheiden. Dieses zeigt dem Lagerpersonal, welche Waren in welchem Umfang benötigt werden und schafft die Grundlage für die Buchung von Warenein- und -ausgängen zur Aktualisierung des Lagerbestands. Die Möglichkeiten reichen von einer einfachen Artikelliste zum Abhaken bis hin zu RFID-basierten Hightech-Lösungen. Nachfolgend ein Überblick über gängige Kommissioniermethoden:
- Pick-by-Paper ist die einfachste Form der Kommissionierung, bei der das Lagerpersonal eine ausgedruckte Pickliste nutzt, um Artikel abzuhaken und die Daten später in EDV-Programme zu übertragen.
- Pick-by-Scan ist eine häufig genutzte Kommissioniermethode, bei der Aufträge auf einem Mobilgerät angezeigt und durch Barcode-Scannen erfasst werden; die Datenübertragung erfolgt in Echtzeit an die Lagerverwaltungssoftware.
- Pick-by-Voice ist eine sprachgesteuerte Kommissioniermethode, bei welcher Mitarbeitende über ein Headset Anweisungen erhalten und die Warenentnahme bestätigen, auch hier erfolgt die Datenübertragung in Echtzeit.
- Pick-by-Light erfordert eine spezielle Lagereinrichtungen mit Lämpchen, Mengenanzeige und Bestätigungsknopf an den Regalen. Diese zeigen an, wo Ware entnommen werden soll und aktualisieren den Warenbestand.
- Pick-by-Vision nutzt Datenbrillen, um alle relevanten Informationen anzuzeigen und aufzuzeichnen. Die Brille erkennt das Blickfeld des Mitarbeiters, zeigt benötigte Details an und überprüft die Entnahme automatisch, wobei sie die Menge und Art der Waren mit der Bestellung abgleicht.
- Pick-by-RFID ist ein Kommissionierverfahren, bei dem Artikel mithilfe von RFID-Tags kontaktlos identifiziert und verfolgt werden bei gleichzeitiger Datenübertragung an Lagerverwaltungssysteme.
- Pick-by-Watch ist ein belegloses Kommissionierverfahren, bei dem Lagerpersonal Aufträge über eine Smartwatch erhält, Artikel entnimmt und Bestände in Echtzeit an die Lagerverwaltungssoftware übermittelt. Die Smartwatch ist dabei mit einem Smartphone verbunden, das als Schnittstelle zum System dient.
- Pick-Pack kombiniert die Entnahme der Produkte aus dem Lagerregal mit dem sofortigen Verpacken der Warensendung.
Das Verfahren Pick-by-Paper steht für die beleghafte Kommissionierung, weil jeder Schritt schriftlich dokumentiert und anschließend mithilfe dieser Belege in den entsprechenden Registern und/oder Programmen vermerkt wird. Das hat den Vorteil, dass weder aufwendige Planung noch technische Hilfsmittel für die Kommissionierung nötig sind und neues Personal schnell in die Aufgabe eingearbeitet werden kann.
Aus der Überzahl der MDE-gestützten Verfahren lässt sich jedoch ableiten, dass die beleglose Kommis-sionierung häufig bevorzugt wird. Besonders in großen Lagern mit hohen Umschlagszahlen hat sie viele Vorteile: Durch beleglose Kommissionierung reduziert sich der Verwaltungsaufwand und auch die Feh-lerquote deutlich, weil wichtige Informationen direkt an die entscheidenden Stellen übertragen werden. Das wirkt sich positiv auf die Kommissionierzeiten und langfristig auch auf die Lagerkosten aus. Ande-rerseits sind mit der Einführung belegloser Kommissioniermethoden hohe Investitionskosten verbunden, die für viele KMUs in keinem Verhältnis zu ihren Einnahmen stehen. Aus diesem Grund werden beide Verfahren voraussichtlich auch in Zukunft nebeneinander bestehen.
FAQ zur Kommissionierung
Die Kommissionierung ist ein Bereich der Intralogistik in Unternehmen. Sie umfasst alle Prozesse der Zusammenstellung von Einzelposten einer Bestellung aus dem gesamten Warensortiment. Dazu gehört:
• die Lokalisierung der bestellten Artikel in verschiedenen Lagerzonen
• die Wahl geeigneter Fördermittel, Transportwege, Behälter, etc.
• die Entnahme der Ware aus dem Lagerregal
• die Zusammenstellung der Warensendung
Nachdem alle Artikel aus dem Lager entnommen und gesammelt wurden, erfolgt die Auslieferung an die Kundschaft oder in die Produktion des Unternehmens.
1. Eingang der Bestellung
2. Zusammenstellen des Pickzettels (ggf. unter Berücksichtigung der Wege)
3. Weiterleitung an den oder die zuständigen Picker oder Pickerin (ggf. in mehrere Lagerzonen gleichzeitig)
4. Beschaffung von Förderfahrzeugen und Transportbehältern
5. Weg zum Lagerplatz und Entnahme der Ware
6. Zusammenstellung des vollständigen Auftrags an einer Sammelstelle
7. Übergabe zum Transport
• Pick-by-Paper: Kommissionierung mit Packzettel oder Pickliste
• Pick-by-Scan: Kommissionierung mit mobilem Endgerät und Barcode-Scanner
• Pick-by-Voice: Kommissionierung ausschließlich erfolgt sprachbasiert über Headset
• Pick-by-Light: Leuchten und Anzeigen an Lagerregalen zeigen, welche Artikel in wel-chen Mengen entnommen werden sollen
• Pick-by-Vision: Kommissionierung mit Datenbrille, die relevante Informationen anzeigt und Entnahme der Ware (Art, Menge) prüft
• Pick-by-RFID: Kommissionierung mithilfe von RFID-Technologie
• Pick-by-Watch: Mit Smartwatch und Mobiltelefon werden Waren kommissioniert
• Pick-Pack: Gleichzeitige Kommissionierung und Verpackung für den Weitertransport
Bei der beleghaften Kommissionierung werden alle Schritte mit den entsprechenden Papieren (ausgedruckt und handschriftlich) schriftlich dokumentiert. Anschließend erfolgt die Übertragung in Akten oder EDV-Programme der relevanten Abteilungen.
Bei der beleglosen Kommissionierung erfolgen diese Schritte digital und teilweise sogar in Echtzeit. Dadurch wird einerseits Arbeitszeit für Dokumentation und Verwaltung eingespart, andererseits lässt sich damit die Fehlerquote der Kommissionierung deutlich verbessern.
Bildquellen:
© Jungheinrich AG